With the improvement of living standards, people’s pursuit of individualized housing and home decoration has become more and more unconventional, which has led to the transformation of the traditional decoration industry and the trend of customization. Coupled with the wide application of man-made panels, the market demand for the corresponding woodworking edge banding machinery is also increasing. Let us introduce the classification of edge banding machines:
According to the design concept and structure, the domestic edge banding machine can be roughly divided into two types, the KDT model and the Qingdao model represented by the northern edge banding machine. Because of the structure and cost difference, the market price of the KDT model is much higher than that of the Qingdao model.
1.Qingdao model

2. KDT model
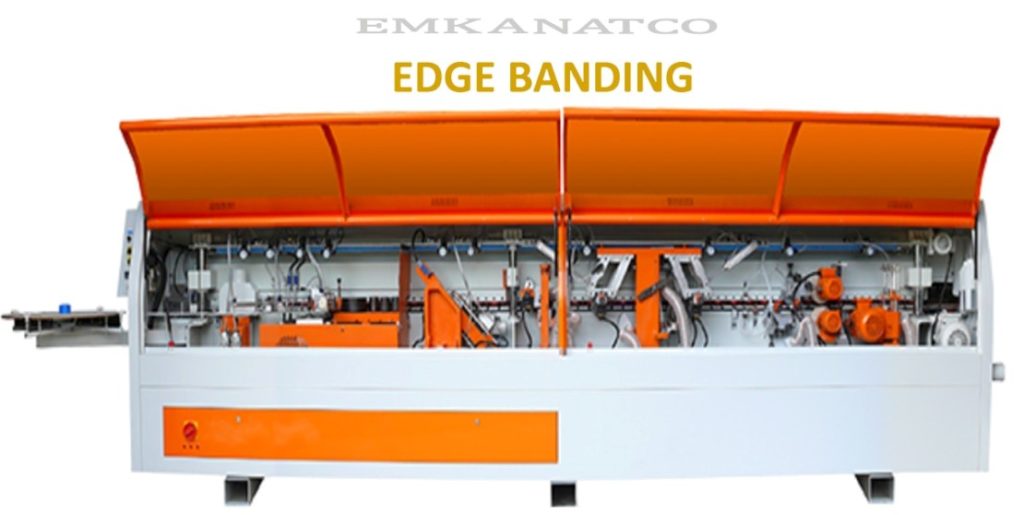
Now let us to introduce those KDT model—MF50F machine details to you.
1. Body structure. The KDT model edge banding machine has a short body, high guide rails, and an overall steel plate thickness of 14 mm, which is weaker than the Qingdao model’s 18 mm thick steel plate. The advantage is that the pressure beam is a wide-seat aluminum profile, which is anodized, and its stability and straightness are higher than those of the Qingdao-style steel plate structure.
2. The glue part. As a key part of the edge banding machine, gluing directly affects the edge banding effect. The KDT model plastic box is fixed by side hanging. Compared with the Qingdao model, the installation accuracy is much higher. The quality of the workpiece is much higher. Both models can directly adjust the overall inclination angle, which is convenient for future maintenance. In addition, KDT adopts thick rubber shaft and intermittent glue feeding is more uniform than Qingdao model. Both rubber shafts must be quenched and tempered by a special process to ensure their hardness and high temperature resistance properties.
3. Belt feeding and pressing structure. The belt feeding and cutting cylinders of the KDT model are controlled by the main air source, and there is no need to adjust the air pressure separately due to different thicknesses. The Qingdao model is the passive wheel controlled by the cylinder, which is different from the driving wheel cylinder of the KDT model. The pressing and sticking part is similar, one active pressing wheel is responsible for the bonding of the edge and the board, and the other passive pressing wheels are responsible for pressing the edge to make it more firmly bonded to the board.
4. End cutting functions. In the early stage, the Qingdao model adopted a double-rail tracking structure. Due to the large number of inductive switches and complicated debugging, most of them were changed to the same single-rail structure of KDT later, which has lower requirements on the size of the plate and more stable effect. Due to the high-frequency motion of the front and rear, the pneumatic and electrical coordination is particularly important, so the accessories are mostly imported brands to ensure the stable and accurate operation.
5. Rough and fine trimming function. This is also the biggest difference between the two models. The working principle is basically the same. When the plate passes through this position, it contacts the profiling wheel and the inclined wheel at the same time, so that the trimmer can be trimmed by the mold and the trimming effect can be achieved. Among them, KDT model is to adjust the straight-line distance between the reclining wheel and the trimmer to convert the trimming amount using different thicknesses. Compared with the Qingdao model, it is more convenient and accurate to directly adjust the trimmer and the copying wheel. KDT’s fine trimming is mostly inclined angle repair, the structure is complex, and the assembly precision is high, which also promotes the cost to be higher than the Qingdao model.
6. Corner trimming function. Due to the location defect of the Qingdao model, this function cannot be implemented for the time being. Corner trimming is mainly composed of high-frequency and high-speed motors, combined with cylinders, and this function is to achieve the effect of profiling and chamfering. It has higher requirements on the stability of the fuselage, the quality of the workpiece, and the assembly and debugging.
7. Scraping and flat scraping function. The working principle of edge scraping is the same as that of trimming, and edge scraping belongs to a powerless mechanical mechanism. The function is to scrape off the wave pattern caused by the high-speed operation of the trimming, so that the trimmed surface is smoother. KDT’s scraping blade is fixed, and the scraping arc and scraping amount can be directly adjusted by the tilt wheel handle. The Qingdao model scraping blade can be moved back and forth through the handle to adjust the radian and the amount of scraping, and the adjustment is more intuitive. The flat scraping function can be installed in both styles. The air cylinder or spring drives the profiling wheel to be close to the board, and the flat knife is close to the board surface, scraping off the excess edge banding and excess glue, making the joint between the board surface and the edge strip more smooth and beautiful.
8. Buffing function. The material of KDT model is thicker and the structure is more stable, which can achieve the buffing effect of deburring. It is worth noting that, please pay attention to the size of the polishing amount. Due to the small power of the motor, if the polishing amount is too large, it will not only scratch the surface of the plate, but also easily burn out the motor due to overload operation.